Boiler Tube Coating: Enhancing Efficiency and Durability
Boiler tube coating is a crucial approach utilized in varied industries to guard and optimize the performance of business boilers. These coatings provide a protective layer on the internal and outer surfaces of the boiler tubes, offering several advantages, together with corrosion resistance, erosion safety, thermal insulation, and chemical resistance. In this article, we will delve into the world of boiler tube coatings, understanding their importance, the types obtainable, and their applicability to different sorts of boilers.
Understanding Boiler Tube Coating
Boiler tube coating is the process of making use of a specialised protective layer to the inner and outer surfaces of the tubes that constitute the boiler system. The primary function of this coating is to safeguard the tubes from the harsh operating conditions inside the boiler. These circumstances usually include high temperatures, stress, and exposure to aggressive chemicals and gases.
The Importance of Boiler Tube Coating
Industrial boilers play a crucial position in varied functions, from power generation to heating in manufacturing facilities. To guarantee their optimum efficiency and longevity, it's important to guard the boiler tubes from degradation. Boiler tube coating provides several important benefits:
1. Corrosion Protection
Corrosion is a prevalent issue in boilers, especially when water is present in the system. Boiler tube coatings create a barrier between the tubes and the corrosive parts, preventing rust and corrosion.
2. Erosion Resistance
The circulate of high-velocity gases and liquids inside the boiler can cause erosion of the tube surfaces over time. Coatings with erosion-resistant properties act as a defend, lowering wear and extending the tubes' lifespan.
3. Thermal Insulation
Some boiler tube coatings present thermal insulation properties, reducing heat loss throughout operation. This enhances the boiler's power efficiency and results in potential cost financial savings.
4. Chemical Resistance
Certain industrial processes produce aggressive chemical substances that can corrode the boiler tubes. Coatings with chemical resistance protect the tubes from these dangerous substances, increasing their durability.
Types of Boiler Tube Coatings
Various kinds of coatings can be found for boiler tubes, every catering to particular necessities. Some widespread varieties include:
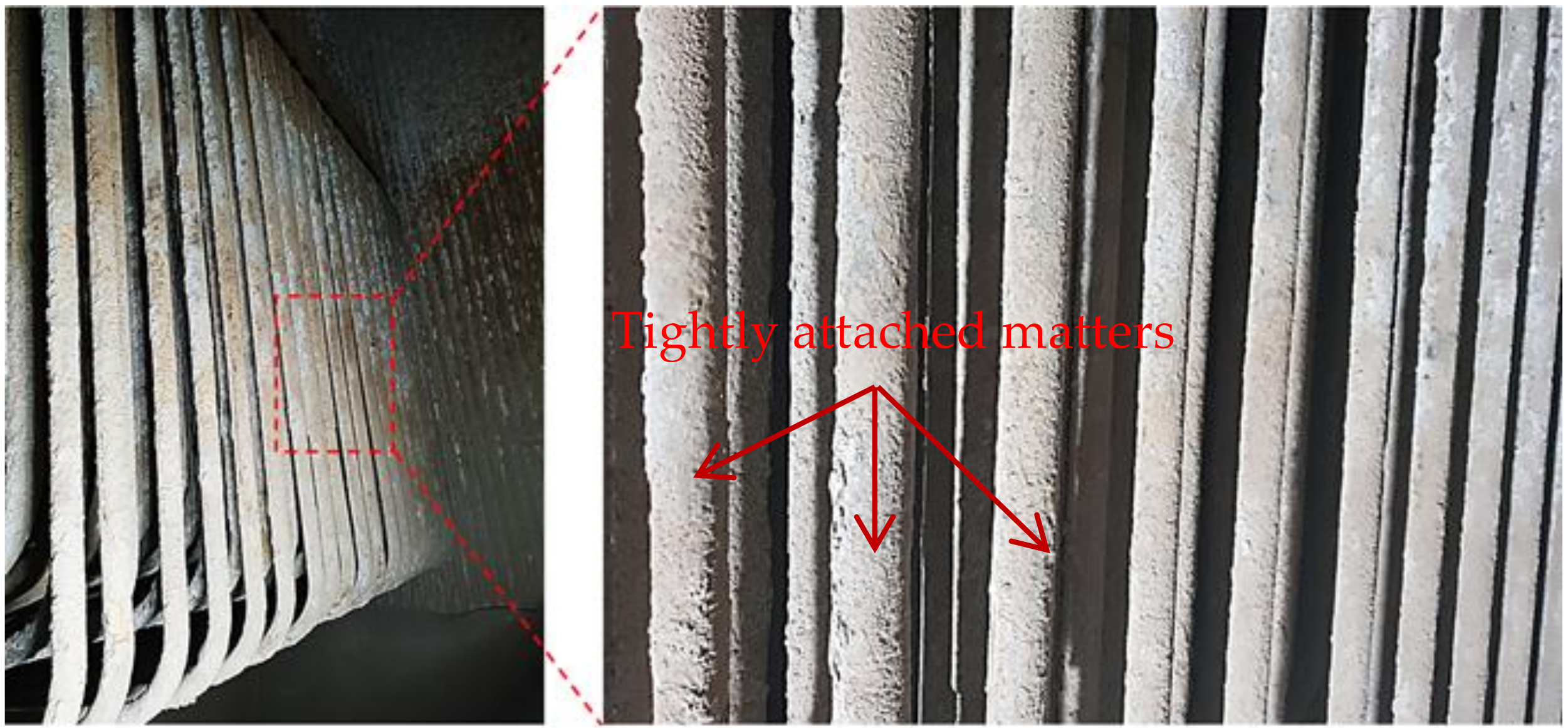
1. Ceramic Coatings
Ceramic coatings provide wonderful thermal and chemical resistance, making them suitable for boilers operating at extremely high temperatures and exposed to aggressive chemicals.
2. Polymer Coatings
Polymer-based coatings provide efficient corrosion and erosion safety. They are relatively straightforward to apply and discover wide applicability in varied boiler systems.
3. Refractory Coatings
Refractory coatings excel in heat resistance and are perfect for boilers where high-temperature combustion occurs.
four. Inorganic Coatings
Inorganic coatings are recognized for their longevity and resistance to oxidation, making them suitable for high-pressure boiler applications.
Applicability to Different Types of Boilers
Boiler tube coating is highly helpful for many industrial boilers, but its applicability might range relying on the particular kind of boiler and its operational situations. Generally, boiler tube coating is suitable for:
1. Water-Tube Boilers
Water-tube boilers, generally utilized in power technology and large-scale industrial functions, greatly profit from tube coatings. The coating protects the numerous tubes carrying sizzling gases and water, ensuring reliable and efficient operation.
2. Fire-Tube Boilers
Fire-tube boilers, present in smaller commercial and residential heating methods, also can benefit from coatings. While the number of tubes is usually lower in fire-tube boilers, the coating offers essential safety against corrosion and erosion.
3. High-Pressure Boilers
Boilers working underneath high-pressure conditions are extra susceptible to stress and wear. Applying appropriate coatings can considerably improve their durability and scale back maintenance requirements.
Maintaining the effectiveness and longevity of business boilers depends closely on boiler tube coating. These coatings' protective layer provides chemical resistance, thermal insulation, erosion safety, and corrosion resistance. By ensuring the boiler tubes are in prime form, this results in higher performance and decrease maintenance costs. Investing in high-quality boiler tube coatings is a proactive move that pays off in the lengthy run, no matter whether or not the sector uses water-tube or fire-tube boilers.